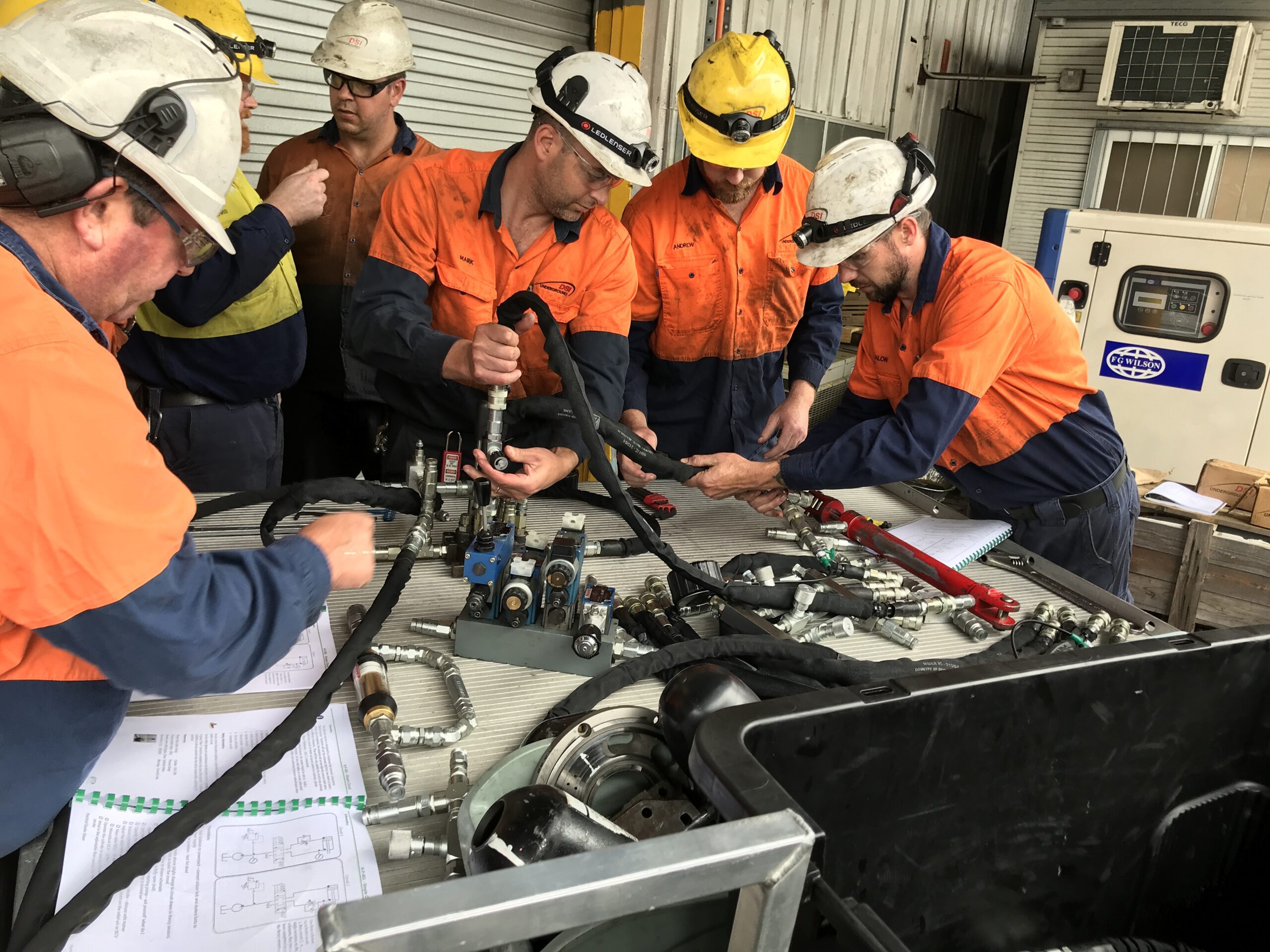
In hydraulic systems, there are key elements that ensure smooth and precise operation. Two critical factors that play a vital role in achieving optimal performance are servo pressure and control pressure. These terms may sound technical, but fear not! In this article, we’ll delve into the fascinating world of servo pressure and control pressure in closed loop systems. Get ready to uncover the secrets that industry professionals use to elevate their hydraulic systems to the next level.
Servo pressure is like the maestro of a hydraulic system, conducting a symphony of forces to achieve precise control. Think of it as the guiding hand that directs the flow of hydraulic fluid to various components within the system. The primary purpose of servo pressure is to maintain a consistent and accurate level of force or torque. By doing so, it ensures smooth operation, prevents system overload, and enhances the overall efficiency.
Servo pressure is achieved through the use of proportional valves, which regulate the flow of hydraulic fluid in response to input signals. These valves act as the control mechanism, adjusting the pressure to meet the desired output. By carefully manipulating the servo pressure, industry professionals can achieve the desired level of precision and responsiveness in their closed loop systems.
While servo pressure takes centre stage, control pressure plays a crucial supporting role in closed loop systems. Control pressure, as the name suggests, is responsible for controlling specific functions within the system. It provides the necessary force to activate various hydraulic components such as cylinders, valves, and actuators.
Control pressure is often achieved through pressure relief valves, which maintain a predetermined pressure level within the system. By carefully adjusting the control pressure, operators can ensure that the hydraulic components function optimally, providing the desired force or movement. This control is essential in applications where precise positioning, speed control, or force regulation is required.
The Power of Closed Loop Systems:
Now that we have a better understanding of servo pressure and control pressure, let’s explore their significance within closed loop systems. Closed loop systems are designed to continuously monitor and adjust the output to maintain the desired performance. They provide a feedback mechanism that ensures the system operates within the desired parameters, even in the presence of external factors or changing conditions.
Servo pressure and control pressure work hand in hand in closed loop systems to achieve optimal performance. The feedback mechanism constantly compares the desired output with the actual output, making minute adjustments to the servo pressure and control pressure as necessary. This dynamic control loop allows for precise and reliable operation, resulting in improved accuracy, reduced energy consumption, and enhanced overall system efficiency.
The benefits of understanding and effectively utilising servo pressure and control pressure in closed loop systems are far-reaching. By harnessing these concepts, industry professionals can unlock a world of possibilities. Here are a few notable benefits:
Enhanced Precision: Fine-tuning servo pressure and control pressure allows for precise control of hydraulic components, enabling accurate positioning, speed control, and force regulation.
Improved Efficiency: By optimising servo pressure and control pressure, closed loop systems can operate with minimal energy waste, leading to improved overall efficiency and reduced operating costs.
Increased Reliability: The continuous monitoring and adjustment of servo pressure and control pressure ensure consistent performance, minimising the risk of system failures and downtime.
Future Expansion: Understanding these concepts lays the foundation for advanced hydraulics training and opens doors to further certifications and career progression.
Servo pressure and control pressure are the dynamic duo behind the scenes of closed loop hydraulic systems. By mastering these concepts, industry professionals can achieve enhanced precision, improved efficiency, and increased reliability. Want to learn more about the differences in how pressure works in closed vs open loop systems? These are core concepts that you will cover in the training you undertake with APT. Comment below if you would like to start your journey to becoming the onsite fluid power guru!